“New Beginning” for the Baobab Scattered Mine Laying Platform
Huta Stalowa Wola, during this year’s edition of the MSPO Defence Exhibition in Kielce, showcased its Baobab-K scattered mine-laying platform, based on a wheeled chassis. The procedure related to implementation of the development works concerning the said vehicle may begin in a few months. Due to the fact that new requirements have been defined, creation of a new vehicle may be needed too. Introduction of a system of this class into the inventory of the Polish Army in larger quantities would enhance the capacity to create mine-fields, which could hamper the movement of the enemy mechanized units.
During this year’s edition of the MSPO International Defence Salon in Kielce, Baobab Platform based on the Jelcz P.662 chassis has been presented. The chassis has been fitted with four mine dispensers. Presentation of the Baobab vehicle is related to the process, in which a will exists to accelerate the implementation of the programme, and to re-initiate the relevant proceedings.
Baobab is a modernized and enhanced derivative of the Inżynieryjny System Minowania [Engineering Mine-Laying System] introduced into use in the Polish Army back in 2004. The said platform was based on a MT-LB family tracked chassis which featured 4 launcher racks with 400 MN-123 anti-tank mines provided by the Bydgoszcz-based Belma company.
In this way, Kroton Scattered Mine-Laying Carrier was created. A small quantity of these vehicles was manufactured by the HSW S.A. company. The aforesaid platforms took part in this year’s military parade, during the Polish Armed Forces Day. Back in 2013, during the MSPO Kielce Defence Exhibition, the Baobab vehicle received the Defender award.
The Initial Tactical-Technical Assumptions (WZTT – Wstępne Założenia Taktyczno-Techniczne) and terms of reference issued by the Armament Inspectorate suggested that there is an expectation that the system is to be used in motorized formations based on wheeled platforms. The mine-barriers created by the system are to correspond with the entries contained within the Rules of Operation for the Engineering Units, according to the Defence Norm NO-02-A49:2013, compatible with the NATO standards.
Even though the requirements stated that the mine-laying platform should be capable of “creating light, medium and heavy anti-tank mine-fields”, it was obvious that the MN-123 mines were going to be the basic asset used within that scope. The MN-123 is an anti-tank mine featuring an EFP shaped charge of twin (two-sided) effect, capable of penetrating 60 mm RHA armour. This – usually – is a level of capabilities sufficient for damaging the tracks of an armoured vehicle and effectively strike the bottom armour of most of the armoured platforms. MN-123 mines have been fitted with a non-contact magnetic fuse with instantaneous or delayed effect, which is active under the whole outline of the vehicle. The fuse is impossible to remove, and it also has an option of programmable self-destruction and self-neutralization within the period of 1 to 30 days. The mines are also detectable, in line with the CCW convention.
The mine is not sensitive to mine detectors, it is also protected from being neutralized with the use of explosive and electromagnetic systems. Explosion of a mine placed next also would not initiate the fuse. A single mine has a shape of a flattened cylinder, with a diameter of 180 and height of 90 millimetres. The mine weighs 3.7 kilograms. Neutralization of a mine barrier created with the use of such mines is time-consuming for the attackers, and this is the basic purpose of this engineering system – to hamper the enemy’s progress.
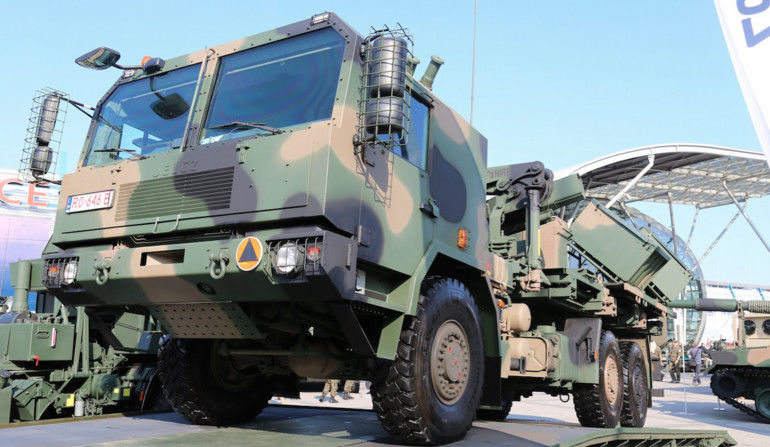
The Baobab system is designed to allow the user to rapidly create minefields of a proper density, with these minefields being capable of destroying or damaging vehicles, including heavy armoured platforms, and force the attacker who has to deal with such obstacle to implement time-consuming procedures required to cross the minefields or to change the direction of attack. The effect which is to be obtained is defined as follows: delayed progress or changed direction of the offensive, forcing the enemy to go around the minefield, and fall into ambushes saturated with anti-tank weaponry, or to go through a difficult terrain (swamps, water obstacles, cliffs). Even if the minefield does not inflict relevant and irreversible damage to the equipment used by the adversary, such barrier still may become an important and effective asset in the process of shaping the tactical situation.
Delaying the offensive and narrowing the space available for tactical manoeuvres for the enemy armoured group may both make it easier to destroy the vehicles or disorganize that unit, with the use of aviation, tube or rocket artillery assets.
Most of the requirements contained in the tactical-technical assumptions were easily complied with by the existing HSW Baobab system, however, some of the parameters of the vehicle were not sufficient or compliant with the assumptions issued by the Armament Inspectorate. The AI defined the carrier platform to come in a form of a “heavy all terrain vehicle fitted with an all-wheel drive, with payload capacity of no less than 10 tonnes, also featuring a loading device”. Baobab, the prototype of which has been undergoing a test programme at the HSW facility since 2010, has been fitted onto a Jelcz P662 wheeled platform which is also utilized as a carrier for the WR-40 Langusta rocket artillery system.
Baobab, manufactured by the HSW facility, features a 2-person armoured cabin, not a carriage-type cabin applied in case of the Langusta launcher, where the crew consists of more persons. A scattered mine-laying platform has been embedded on the chassis mentioned above, featuring 4 sets of 20-barrel MN-123 mine dispensers, containing, in total, 400 mines in 80 cartridges. Baobab also has a variant with six launcher blocks, based on the very same chassis. The smaller version of the scattered mine-laying platform has a weight of 5.5 tonnes (including mines), while the larger variant is heavier - it weighs 6.7 tonnes.
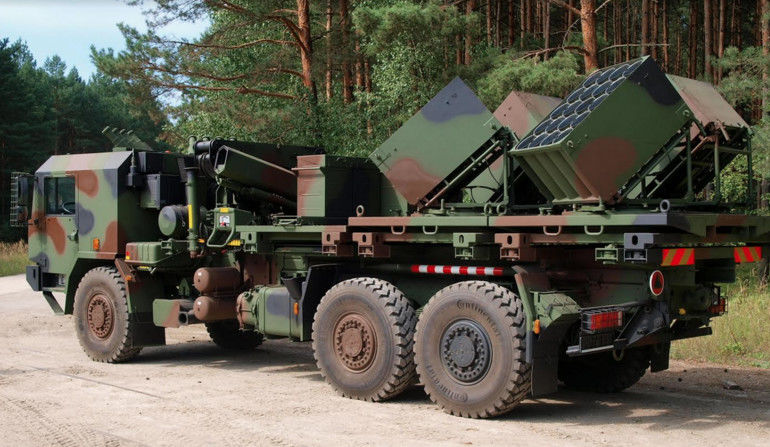
The first prototype of the Baobab platform (under a different name) has been presented by HSW during the MSPO event in September 2007, three years before the Armament Inspectorate announced the initial tactical and technical assumptions pertaining to this type of equipment. Within that period, HSW was intensively looking for a product which could be manufactured for the Army, since the Krab self-propelled howitzer programme was suspended, while the Rak mortar programme was still at the very early stage of development at the time. The mine-laying platform presented there was placed on a 3-axle Jelcz chassis, and it was fitted with a self-loading system and six mine-launching blocks. The current scattered mine-laying platform, instead of a highly mobile 3-axle chassis features 4-axle chassis with improved offroad capabilities and reduced pressure imposed on a single axle.
The Armament Inspectorate also required the Baobab-K system to be fitted with loading equipment, control suite, UHF radio with parameters no worse than the ones seen in case of the TRC9500 radio, and finally, the vehicle was also to be fitted with 81 mm smoke grenade launchers. The system was to enable the crew to reload the mine dispensers autonomously, when loaded from a truck or a trailer, in time no longer than 30 minutes.
The condition which – according to HSW – was too difficult to be met due to technical reasons was the requirement, according to which the platform was to be fitted with a remotely controlled turret unit featuring a .50-cal machine gun – ZSMU-1276A1 Kobuz (also known as Tumak-4), with minimum ammunition capacity of 800 rounds. Representatives of the HSW company claim that such solution would be costly and that the vehicle will not be operated in conditions in which direct enemy contact would be the case. Moreover, the scattered mine-laying platform was to be removable. Then, the vehicle was to be capable of carrying out transport tasks, with an option of loading and transporting 20-feet containers, and towing a trailer with additional mine-laying unit.
The procedure, which involved a single entity, ended up in a fiasco. According to the release issued by the Armament Inspectorate, a consortium, involving the following companies: HSW S.A. as a leader, Jelcz Komponenty Sp. z o.o, BELMA S.A., WB Electronics, AREX Sp. z o.o and Military Institute of Technical Engineering; did not meet some of the formal requirements.
The tender was cancelled and restarted, with deadline for finalizing the works set on 28th November 2014. The assumptions and requirements remained largely unchanged. Ultimately, within the framework of the development works related to the platform, the stage within which the design tasks were to be determined was documented, with a budget of no more than PLN 500 thousand. The aforesaid consortium became an entity which performed the relevant works, on the basis of a contract concluded on 30th June 2014. In August 2015 the Armament Inspectorate initiated the tender proceedings, the goal of which was to select the contractor who would be responsible for designing and developing the new PMN platform. Creating a prototype and technical documentation was the main subject of these proceedings. 31st October 2018 has been defined as a final deadline for performing the works related to that order.
Moreover, some of the requirements were also precisely defined, since the Inspectorate requested the system to be fitted ontoo an 8×8 AWD chassis with an armoured cabin, providing the Level 1 of protection in line with the STANAG 4569 norm. The platform was to be fitted with 6 electrically controlled MN-123 mine dispensers. Moreover, it was said that platforms, on which the launcher racks are to be placed, are to take the combat or transport position with the use of a specifically designed hydraulic system. An option was to be available for the platforms to be dismantled via an autonomous loading system.
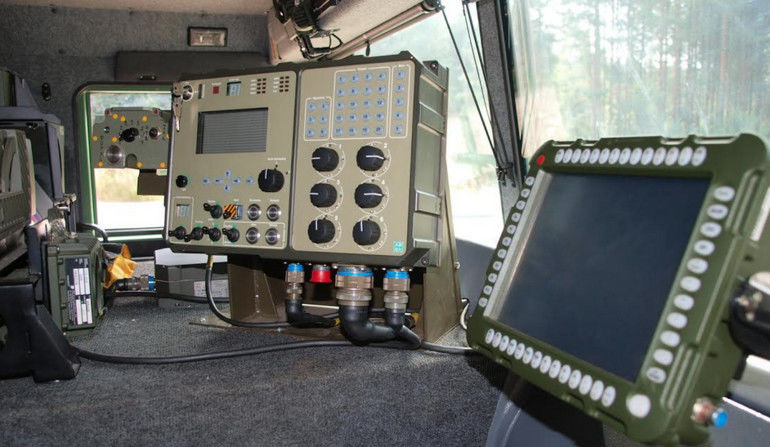
The platform, according to the aforesaid requirements, shall “be fitted with an ICT system that would make it possible to control the mine-laying process in manual and automatic mode, with visualization of the minefield on a digital map, with an option of automatic reporting (via the VHF) radio, referring to the created minefield and its parameters”. The entry pertaining to the Kobuz armament module has been kept within the requirements. No request that was not excluded was submitted in a response to this announcement until the set deadline of 22nd September. The procedure was restarted on 9th November 2015. Also, in this case, the procedure did not end up with selection of an offer.
At a certain stage, HSW, acting as the leader of the consortium, has limited its involvement in the programme. This happened not only because of the fact that the company was burdened with work on other strategic programmes, as besides the programmes which already are entering the production stage (Rak self-propelled mortar, Krab howitzer), a lot of potential is used to carry out the works related to the ZSSW-30 unmanned turret, Kryl howitzer and a new amphibious Borsuk IFV. Moreover, even though HSW is no longer a leader of the consortium which works on that programme, the company is still involved in the development activity related to the WR-300 Homar rocket artillery suite.
Above all, it was hard to determine whether and what impact was the involvement in the “Baobab-K” programme going to have on prospective contracts and business, and what potential would be required by the HSW to be provided by the members of the consortium, within the scope of involvement related to series production of such systems. According to the representatives of the HSW company, no analysis provides a comprehensive answer to the question referring to the role of the said system in the structure of the motorized/mechanized brigade, and what quantitative needs would be defined, when it comes to this mine-laying platform. Hypotheses claiming that 12-15 examples would be needed are equally credible as those, saying that around 50 mine-laying systems would be ordered. Within the recent months, a thesis emerged suggesting that Baobab-K platform would become a relevant component within the Territorial Defence units.
From the HSW’s point of view, difficulties were also caused within the scope of meeting the initial tactical and technical assumptions pertaining to the range of tests required to be carried out during the work, and to the related costs. At most stages of the R&D works (model and prototype), the research was carried out in a way which would provide full compliance with the tactical and technical assumptions. In other words, the model would be required to undergo the same test programme as the one applied in case of the prototype which was to be developed later. With all, financial and time-related, consequences of that fact. Each of the test packages required a full package of MN-123 training mines to be used, according to the specification of the tender. This created more, significant costs.
According to the unofficial sources close to the Ministry of Defence, the Polish Armament Inspectorate is planning to make, soon, yet another attempt to tackle the same problem. The aforesaid steps were preceded with an audit carried out by PGZ, pertaining to the progress achieved so far, and a chance to avoid further complications.
The suggestions have already been sent to the administrator of the programme. Moreover, it is postulated that the mine-laying cartridges do not have to undergo testing, since they are already being operated by the Army within the Kroton system. HSW and Jelcz also propose that the vehicle used for scattered mine-laying is armed with a .50-cal machine gun mounted in an open station at the top of the cabin. Such solution would replace the required remotely controlled armament module. The remotely controlled armament module weighs around 200 kilograms, thus, in order to achieve a proper level of rigidity of the cabin the structure would have to be reinforced, which consequently increases the weight of the cabin, the vehicle, and makes the structure of vehicle much more complicated and more expensive at the same time.
Obviously, each of the aforesaid solutions has its advantages and disadvantages, and reaching a compromise here, with a reference to the role of the vehicle, would be required, also in relation to the expected use in combat etc. Similarly as in case of the ZSMU module, there is another issue pertaining to the OBRA-3 sensors which act as a laser warning receiver, and which are to be displaced around the edges of the mine-laying platform which, according to the requirements issued by the Armament Inspectorate, is to change its configuration, depending on the phase of operation. Representatives of the HSW company claim that there is an option of resigning from such formula of self-defence system, and implement a manual control system for the smoke grenade launchers, at the station of the mine-laying systems operator. There are several similar proposals.
Another problem is seen in the procedures, within which the stages of the proceedings are to be realized. The requirement to proceed in line with the Public Procurement Law, and the guidelines related to the requirements of carrying out all the tests at certified centres and institutes also creates some difficulties. In some cases, the cycle between sending the vehicle for tests, and obtaining the final test approval, lasts around a year. The contractor has a limited influence on the timeline formed by the terms above, and at the same time he is obliged to meet the conditions arranged within the agreement concluded with the ordering party.
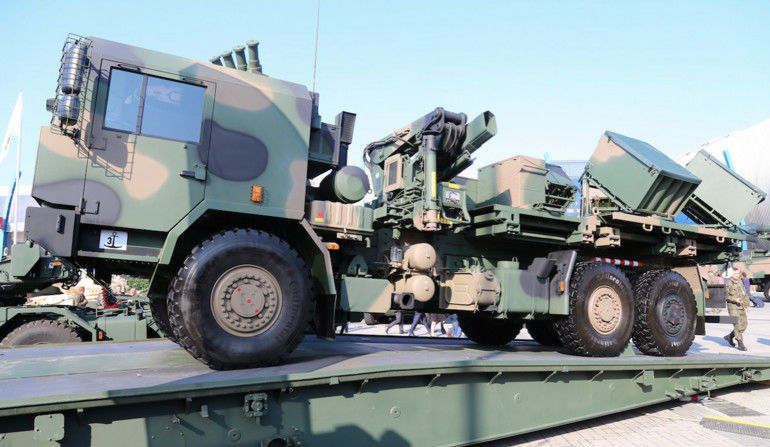
According to the representatives of the HSW company, the three-year long period within which the works are to be finalized may turn out to be insufficient, if, according to the assumptions, the vehicle is to cover the same path once as a model, and once more, during the prototype testing stage. This is the source of the concept, assuming that model tests concerning the compliance with all of the Armament Inspectorate’s requirements, shall be carried out in conditions and at certified centres in a way which would make it possible to transfer the results of this research automatically, once certain conditions are met, to the prototype test programme, and to approve them then.
When one carries out an analysis of the published assumptions, a conclusion may be reached that within the R&D works, the goal of which is to create the Baobab-K scattered mine-laying platform, it would be unavoidable to create a brand new vehicle from a scratch, different from the existing Baobab platform which is owned by HSW and which was presented during the MSPO event. It is imperative that the system is to be fitted with 6 dispensers hosting, in total, 600 mines, and HIAB loading system, which automatically requires the manufacturer to use an 8×8 layout. The cabin, when compared to the existing prototype, must also be modified within some scope. No precise requirements were set, e.g. as to whether a bed should be fitted within the cabin or not. The landmine-laying platforms are to take the firing position with the use of hydraulic actuators, and the individual launchers are expected to be driven electrically. Moreover, relevant changes are also required to take place in the control section of the mine-laying panel, within which numerous functions referring to the minefield layout are to be automated.
In the current system which has an option of working in an automatic mode, or in a mode in which full manual control is yielded by the operator, the parameters of the minefield visualized on a computer screen are transferred, in line with the NATO standards, via a radio connection, to the higher levels within the chain of command. The new system which is to be installed onboard the Baobab-K mine-laying platform will provide the user with a possibility of computing the parameters of the minefield, once an order is received to cover the specific area with mines. The system is to work in both ways. Even though the assumptions of the programme do not expect a command vehicle to be embedded within the structure of the units, the applied solution means that a greater degree of autonomy is provided for each of the vehicles operating within the battlefield.
The vehicle is currently fitted with the GPS navigation suite and odometer, onboard computer with visualization terminal based on a digital map, VHF FRC9311 radio and FONET internal communications system, along with a panel for controlling the mine dispensers and smoke grenade launchers (8), along with proper testing systems for the mine cartridges. A training system may also be fitted onto the platform. Baobab-K is to be even more advanced.
If everything goes in line with the expected timeline, namely when the procedure is initiated within the period of the upcoming 2-3 months and when the agreement is concluded at the beginning of 2017, the prototype of the PMN Baobab-K vehicle, in its final variant, with finalized qualification tests programme and technical documentation required to initiate mass production, shall be ready in 2020. Within that time, a new chassis needs to be designed, created and tested, along with the mine-laying platform control systems and the ICT system including mine dispensers control software, and modules that would make it possible for the ICT solutions to act together with the communications and data exchange suites.
According to the requirements defined by the Armament Inspectorate, PMN Baobab-K system should be capable of creating minefields with the use of the scattering mine-laying method, in any weather conditions, with a depth which would not be smaller than 180 meters. The vehicle should also be able to cover the strip behind it with mines, with the use of three types of the MN-123 anti-tank mines. The required density of the minefield is to be defined by the vehicle commander, at level of 0.15 to 1.2 landmines per linear meter, and then it should be achieved automatically by proper setting of the dispensers and the control system which processes the information related to the position of the launchers and the actual speed of the vehicle.
Once the system receives the data related to the type of the mines, the control system may present the operator with information related to selectable self-destruction periods for the mine, if such information has been introduced into the control suite’s memory. The system is also to offer an abort option, referring to the mine-laying process. Determining the vehicle’s position, and visualizing it on a digital map is to be made possible thanks to a GPS system, with accuracy of 10 meters.
Through the control system, GPS system and VHF radio, the report pertaining to the parameters and location of the established minefield, time setting and self destruction time, and current options related to further mine-laying depending on the quantity of mines remaining on the vehicle, is going to be received by the commander of the platform, who, at the same time, is going to act as the operator, gunner and, should a need arise, as the driver. Then such information may be transferred up the command chain.
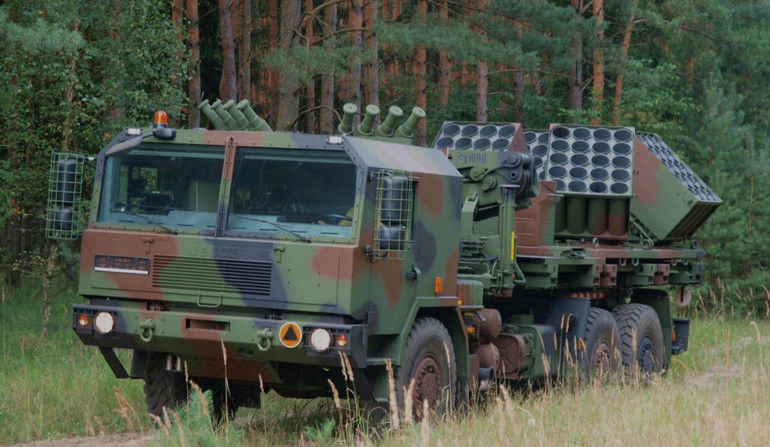
The Armament Inspectorate also expects the platform’s carrier to be operable after the tyres are shot, or after the vehicle runs over an anti-personnel mine. The wheels shall make it possible to use the vehicle once the tyres are shot or damaged, and when pressure goes down to zero, at a distance of at least 50 kilometres with speed of 50 kilometres per hour. The platform is also to feature a limited visibility system utilizing proper lighting, multi-spectral Berberys camouflage system and protective/camouflage paint cover.
For the consortium, especially for the HSW company, working on the Baobab-K mine-laying platform may constitute a training before undertaking prospective development works on the PMN Baobab-G or Kroton II systems. This is the probable name for the new version of the scattered mine-laying platform which could be tailored to operate together with heavy armoured units. It may come in a form of a modernized and perfected variant of the Kroton platform, based on the Krab’s K-9 chassis. The weight of the body formed by the mine-laying platform featuring 6 launchers of around 10 tonnes is much lower than the mass of the turret system of the Krab howitzer, hence designing a Krab-chassis scattered mine-laying system in a short period of time should not pose a problem.
To make it even more interesting, works on such vehicle may be carried out as a formal procurement procedure with adjustment, with a type-rating state test programme, which would eliminate the complicated R&D procedure. Such Baobab-G (or Kroton II) vehicles may significantly increase the combat potential of the armoured units using the modernized Leopard 2PL, Leopard 2A5 main battle tanks, Krab howitzers and new IFVs.
At the moment, the existing Baobab system may create the minefield when moving at speeds ranging from 5 to 25 kph, hence creating a minefield 30-90 meters wide, on the side of the vehicle, or behind it, takes around 15 minutes - 22 minutes in case of the version with 6 dispensers, assuming that the vehicle is operated by a crew of 2. The time required to reload the mine dispensers should not be longer than 20 minutes (30 minutes for the variant with 6 launchers). Once the procedure is completed, Baobab may proceed and carry out next task. Nonetheless, meeting all of the requirements defined by the Army requires more work to be carried out.
Jerzy Reszczyński
WIDEO: Defence24 Days 2025: Premier Defence & Security Conference in CEE