Testing and research of hydropneumatic suspension modules
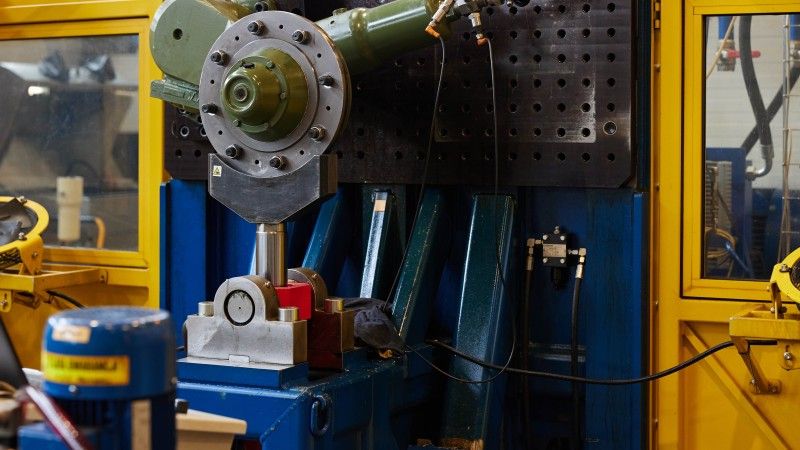
Photo. PONAR Wadowice S.A.
In industry, and especially in the arms sector, precise and reliable testing of components is crucial. In the case of hydropneumatic systems and suspensions, which operate in extreme conditions, simulating real operating conditions is essential. Having the ability to replicate such conditions on the test shop floor allows for precise analysis of component behaviour and ensures their reliability during actual operation in military vehicles.
A Sponsored article
Hydraulics plays a key role in military vehicles such as tanks, self-propelled howitzers, armoured personnel carriers, mobile radar stations and ships. Hydraulic systems drive key mechanisms and ensure that they can be controlled quickly and efficiently. The ability to fully replicate real-world operating conditions on test stands allows the reliability of these systems to be verified under extreme battlefield conditions.
It is important to remember that hydraulic equipment on military vehicles must be resistant to environmental factors, while at the same time responding quickly to the operator’s commands. This is particularly important in the case of suspension systems, which maintain mobility in difficult terrain and stabilise weapon systems. Any failure or delay in operation can have a direct impact on the success of the mission and the safety of the crew.
In harsh combat environments vehicles are exposed to climatic and mechanical factors (frost, ice, dew, dust, etc.) and corrosion resulting from the effects of salt spray on equipment. In the latter case, it is necessary to use rust-resistant materials and special protective coatings.
Read more
In the realities of combat, military vehicles, and therefore their hydraulic systems, operate at the limit of their capabilities, which is why material fatigue occurs. It is therefore essential to ensure their reliability over a long service life, and especially to ensure that they are resistant to shocks, impacts and vibrations that destabilise their operation.
At the PONAR Wadowice Research and Development Centre, real operating conditions are simulated, and the tests carried out allow engineers to verify the performance of individual components in conditions that mimic extreme operating scenarios.

Photo. PONAR Wadowice S.A.
Among the verification tests are those of hydropneumatic suspensions under cyclic loading conditions. By seeing how the hydraulic equipment behaves, improvements can be made to increase crew safety and efficiency. Above all, the strength of all components and the response to dynamic loads are tested, minimising the risk of failure at critical moments. Each project made for the defence sector requires an individual approach, especially because of the need for an exact replication of specifications and operational requirements. Tests and simulations carried out at Ponar allow the customer to verify product performance in real time, as well as to conduct remote acceptance, which is important for large international projects.
Test benches must not only be prepared for the customer’s specific requirements, but also comply with international norms and standards (defence standards, national guidelines, AQAP). Hydraulic systems used in military vehicles undergo rigorous testing to confirm their ability to meet operational requirements under combat conditions. They are designed in such a way that they must confirm that the products comply with the applicable standards, as this is key to obtaining certification of the products for use by the armed forces. It must be added that the testing process requires ongoing collaboration between both parties to ensure that all stages of testing comply with the agreed specifications.
Read more
- PONAR: Polish Solutions for the IndustrySponsored
Test benches and the testing process itself must be adapted to the operational requirements of the customer, which usually means testing according to an imposed procedure or confirming compliance with a reference product. Collaboration enables ongoing adjustments, which is important especially in the context of rapidly evolving military systems.
A significant facilitation of the collaboration is the possibility to remotely monitor testing and product acceptance. Even without being physically present in the factory, customers have complete overview of the testing process thanks to highly advanced data recording and analysis tools. Not only can the customer evaluate the test parameters on an ongoing basis, but also to change the requirements if new guidelines arise related to, for example, defence or national standards. Positive final tests confirm the compliance of the product with the requirements, which provides a guarantee of reliable operation of the supplied hydraulic components under combat conditions.

Photo. PONAR Wadowice S.A.
Finally, we would like to add that at PONAR Wadowice testing takes place on three different categories of test stands:
Strength stations: used mainly for pressure tests (at pressures of up to 1,000 bar) and tests under extreme conditions, such as in climate chambers (at temperatures of -52° C and +7° C). Such tests are designed to test whether components can withstand maximum loads and extreme temperatures and humidity.
Read more
- PONAR - Dual Use HydraulicsSponsored
Fatigue test benches: focus on the analysis of the long-term strength of materials under repeated loads (up to 70 tonnes). In such test benches, thousands or even millions of duty cycles are simulated to predict when and under what conditions a component may fail. Hydropneumatic suspension modules, for example, may have just been subjected to millions of duty cycles to see if fatigue will set in or a component will wear out more quickly.
Acceptance workstations: these are used to check that the finished products are properly made and working. Before a component is put into service, it must pass a series of tests to confirm that it meets all technical and quality requirements. The tasks of these stations include carrying out functional tests to confirm that the characteristics of the components comply with the required values. This can include, for example, operating pressures, actuator forces (up to 70 tonnes) or torques (up to 7,500 Nm), as well as verification that the component is within defined tolerance limits (e.g. in the case of pumps, this is the recording of operating characteristics and comparison with a benchmark).
A Sponsored article