Suspension of the future from a Polish company [ANALYSIS]
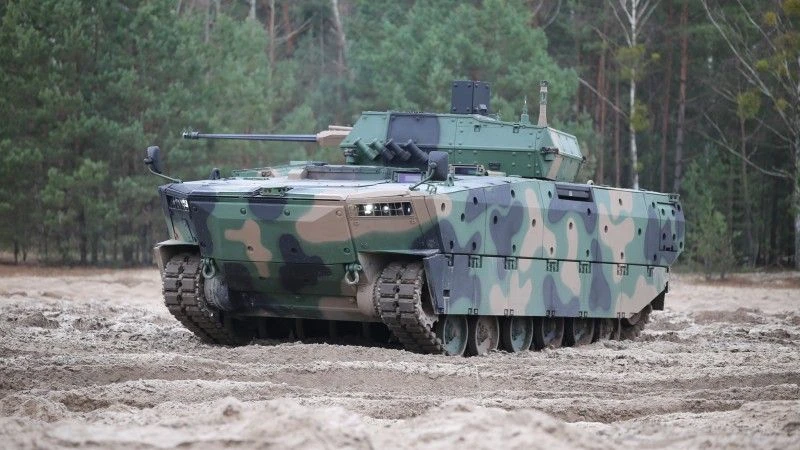
Photo. Marcin Ordon / Defence24
Hydropneumatic suspension is becoming the new standard in armoured fighting vehicles. The leading Polish entity in this rapidly growing market segment is PONAR Wadowice.
Sponsored article
Large purchases of heavy equipment for the Polish Armed Forces are not just an investment in Polish security. It is also an opportunity for the domestic defence industry, which has received strong impetus for development. One of the fruits of this process are hydropneumatic suspension modules developed and manufactured by PONAR Wadowice. The work of Polish engineers is not only a reflection of global trends in combat vehicle design, but also a solution with considerable development potential.
The best way to demonstrate the advantages of hydropneumatic suspension is to compare it to a solution that, until recently, was the global standard. For many decades, the most common suspension arrangement on AFVs was trailing arms sprung by torsion bars. One could hardly come up with a better point of reference to illustrate the scale of progress that has been made in the field of AFV running gear.
Why not torsion bars?
The popularity of torsion bars as a spring element in armoured fighting vehicles stems from several factors. It is a technically simple solution, with documented effectiveness and great durability. Torsion bars have sufficient load-carrying capacity to be used in very heavy vehicles, such as modern main battle tanks. They are also capable of absorbing and dissipating large amounts of the energy generated by the movement of a tracked vehicle.
However, this solution also has significant limitations. The main issue is the space that needs to be provided inside the vehicle. The most logical location for torsion bars is at the bottom of the hull, perpendicular to its longitudinal axis. On one side the torsion bar is attached to the side of the hull and on the other side it is connected to the wheel assembly (trailing arm together with the road wheel). The hull has to be tall enough to ensure easy crew access to the torsion bars without having to take the entire vehicle apart. This translates into an increase in hull weight compared to a vehicle with externally mounted suspension bogies.

Photo. st. chor. sztab. Arkadiusz Dwulatek / CC DO RSZ
In addition, the presence of torsion bars makes it difficult to design the bottom of the hull with crew escape hatches. It is not uncommon for the bottom of the vehicle to be penetrated as a result of the detonation of an explosive charge under the hull. A damaged or ruptured torsion bar can become a sizable piece of shrapnel, posing a serious risk to the vehicle’s occupants.
Torsion bars usually take up the entire width of the hull. At the same time, the longitudinal axis of the torsion bar is also the axis of rotation of the trailing arm. In order to ensure that the trailing arms on both sides of the vehicle are mounted at the same height, it is necessary to install the torsion bars in pairs, one behind the other. This makes it physically impossible for the trailing arms and road wheels on both sides of the vehicle to be symmetrically positioned. This translates into unequal wear and tear of the running gear, and also has a negative impact on vehicle handling.
In such an arrangement, it is impossible to perform an on-the-fly adjustment of suspension stiffness – it is a constant that results directly from the thickness of the torsion bars themselves and the properties of the spring steel from which they are made. The same is true of ground clearance adjustment, which is impossible without mechanical adjustments in the running gear. Active adjustment of the damping force may offer a certain alternative, but the practical effects of this solution are quite limited.
A considerable disadvantage of torsion bars is the difficult maintenance, especially on very heavy vehicles. The size, weight and method of attaching the component to the bottom and sides of the hull mean that replacing a damaged torsion bar (for example, one cracked due to wear or corrosion) takes a great deal of time and effort. This has a direct impact on the readiness of the vehicle and its crew to carry out their tasks.
Various torsion bar modifications have been developed to address the many disadvantages of this solution, such as vehicle asymmetry or linear resistance to suspension travel. However, due to a number of factors, none of these ideas have become widespread enough to become the industry standard.
One module, multiple components
A hydropneumatic suspension module for tracked vehicles is a multi-purpose device. Its primary function is to act as a suspension arm that controls the movement of the road wheel in the vertical plane. A gas spring is mounted within the suspension module. This is filled with gas (usually nitrogen) and hydraulic oil, which are separated by a diaphragm. This element replaces the traditional torsion bar, coil spring or leaf spring. A hydraulic shock absorber is also built into the module.
The movement of the control arm causes the nitrogen pressure in the gas spring, which has a non-linear resistance to deflection, to increase. In simple terms, the stiffness of the suspension increases with the travel of the control arm. This slows down the control arm’s rotational movement, converting the mechanical energy from its rotation into hydraulic energy. In this way, it acts as a buffer that softens the movement of the road wheel assembly. The operating characteristics of this system make it unnecessary to use a hydraulic bump stop, which in torsion bar systems is a physical limit to the movement of the control arm.
Hydropneumatic suspension dampens bumps more effectively than a torsion bar system. This contributes to improved traction in all conditions. The average off-road speed is higher, the running gear returns to a neutral stance more quickly, the stabilisation of the main armament and optoelectronics works less intensely, and the soldiers on board (especially dismounts on board an infantry fighting vehicle) are less affected by uneven terrain. This is perfectly illustrated by the smoothness and speed with which a 48-tonne Krab self-propelled howitzer moves off road.
Hydropneumatic suspension has other advantages. The modules are mounted on the outside of the vehicle. This eliminates the need for additional space in the hull for torsion bars. In addition, the modules are only slightly larger in all dimensions than traditional trailing arms, so there is no need to narrow the hull to a certain width. This is extremely important in the face of „hard” limits, such as the maximum dimensions of a vehicle transported by rail or on public roads.
In addition, in the event of failure or a worn out component, it is possible to remove the complete control arm assembly and install a new one without dismantling the module. The damaged component can be sent back to a repair facility for remanufacturing, sent to a military storage facility, and then be fitted to another vehicle in need of repair. This kind of closed circuit with spare parts is somewhat reminiscent of the way in which modern armed forces use quick-change powerpacks for tracked vehicles. This is a major logistical boon for the military, as well as a convenient way to reduce the cost of repairing a key component.
Tracked vehicles do not load the suspension evenly. For example, in a modern infantry fighting vehicle the majority of the weight rests on the front road wheels, because it is in this part of the vehicle where the heavy powerpack and the thickest armour are located. By adjusting the gas pressure in the spring (which also enables ground clearance adjustment) and the damping characteristics of the shock absorber, it is possible to adapt the suspension module to the operating conditions of a particular road wheel.
The absence of torsion bars gives the designer more freedom in forming the shape of the hull and locating components within the vehicle. There is no obstacle to the bottom of the vehicle being reinforced to increase the level of mine protection or to locate crew escape hatches there. In addition, the sides of the hull can be fully symmetrical, which offsets the problem of uneven wear and tear on parts of the running gear on both sides of the machine.
Unique capabilities
Few companies in the world have the capacity to develop hydropneumatic suspension modules for tracked vehicles in-house. Recently, the Polish company PONAR Wadowice, which specialises in power hydraulics, has joined this small group. Over the past five years, a self-funded R&D project has been carried out there, resulting in the development and implementation of two types of passive hydropneumatic suspension designed for Polish combat vehicles.
The WHP25 and WHP35 modules are designed for vehicles with an average weight of 25 and 35 tonnes and with six pairs of running wheels (i.e. there are 12 suspension modules per vehicle). The former model was developed for vehicles based on the Light Tracked Chassis developed by Huta Stalowa Wola. These include, among others, the WD (Command Vehicle) and WDSz (Command and Staff Vehicle), which form one of the foundations of the Regina Battalion Fires Module. The second type of suspension is designed for the Borsuk Combat Infantry Vehicle. The predator from Stalowa Wola is currently being prepared for series production.

Photo. Robert Suchy / Defence24
The foundation for this work was the production and localisation of complete hydropneumatic suspension modules for the Krab self-propelled guns from HSW. The experience gained from this programme and the systematic development of the design and production potential at the Wadowice-based company made it possible to create a local solution of this class, without the need to acquire a foreign licence.
Wadowice-based PONAR is a rare example of a company that can independently design, prototype, test and manufacture hydropneumatic suspension modules for tracked military vehicles. Abandoning torsion bars in favour of modern track systems with hydropneumatic modules opens up new design possibilities for Polish designers of heavy military equipment, also in terms of tailoring the suspension to a specific chassis.
The WHP25 and WHP35 suspension modules were subjected to thorough testing before being handed over to Huta Stalowa Wola for installation on vehicles. This verified the reliability and performance of the hydropneumatic suspension arms in low (-30° C) and high (55° C) temperatures, the ability to operate in fresh and salt water, as well as the resistance to high pressures (of the order of 900 bar), vibration and very high humidity (93-98%).
Made in Poland
An equally important factor is the gradual decoupling of the Polish defence industry from foreign licences and imports of key components. Thanks to the work carried out at PONAR, local production and service potential is being built in a market niche that remains undeveloped in most European countries. This translates into the creation of a number of valuable jobs in the country, shortening supply chains, significant logistical facilitation for the military, savings for the taxpayer and building export potential for unique Polish technical solutions.
It is also pleasing that the Wadowice-based company is already working on long-term development of their latest product. The WHP25 and WHP35 modules are passive, i.e. there is no possibility for the crew inside the vehicle to change the suspension characteristics or adjust the ground clearance. PONAR is already researching proprietary active systems in which the settings of the running gear are changed completely automatically, even when the vehicle is in motion. It can be assumed that a semi-active system, in which ground clearance and damping can be adjusted while the vehicle is stationary, will be a stepping stone on the road to active suspension.
The ongoing war in Ukraine has contributed to a significant increase in demand for hydraulics from Wadowice. The scale of this conflict vividly demonstrates the need for a secure supply chain and national competence in areas that can be bottlenecks in the production of heavy military equipment.
Polish demand for the Borsuk IFV alone (as well as specialist vehicles based on its chassis) is estimated at around 1,400 units. To this should be added the Polish Army’s expected orders for heavy infantry fighting vehicles, new-generation wheeled armoured personnel carriers, self-propelled howitzers and many other vehicles.
Polonisation of the running gear in these vehicles is not just an opportunity for dynamic development for the Polish company, but also a necessity from the point of view of the Armed Forces. That is why it is worth keeping an eye on novelties from PONAR Wadowice, a new player in this market segment, which may soon become a major regional player in a specialist industry.
Sponsored article
WIDEO: Defence24 Days 2025: Premier Defence & Security Conference in CEE